The traditional cleaning industry mostly uses chemical agents or mechanical methods. As my country’s environmental protection laws and regulations are becoming stricter and the awareness of environmental protection and safety is increasing, the industrial cleaning of chemicals has become a problem and will be replaced by laser cleaning. Laser cleaning has the cleaning characteristics of non-grinding, non-contact, non-thermal effect and suitable for objects of various materials, and is considered to be the most reliable and effective solution.
Principle of laser cleaning
Laser cleaning technology refers to the use of high-energy laser beams to irradiate the surface of the workpiece to make the dirt, rust or coating on the surface evaporate or peel instantly, so as to achieve a clean process. The laser is no different from the light (visible light and invisible light) around us, except that the laser uses a resonant cavity to gather light in the same direction, and has a simpler wavelength, better coordination and other performance, so theoretically all Light of any wavelength can be used to form a laser, but in fact it is limited by the fact that there are not many media that can be excited, so the laser light source that can produce stable and suitable for industrial production is quite limited. The most widely used are Nd:YAG laser, carbon dioxide laser and excimer laser.
The mechanism of laser cleaning is mainly based on the fact that contaminants on the surface of the object absorb the laser energy, either vaporize or evaporate, or instantly expand by heat to overcome the adsorption force of the particles on the surface and make them detach from the surface of the object, thereby achieving the purpose of cleaning. To sum up, it roughly includes four aspects: laser vaporization and decomposition, laser peeling, thermal expansion of dirt particles, substrate surface vibration and particle vibration; and laser cleaning is often the result of multiple mechanisms acting simultaneously.
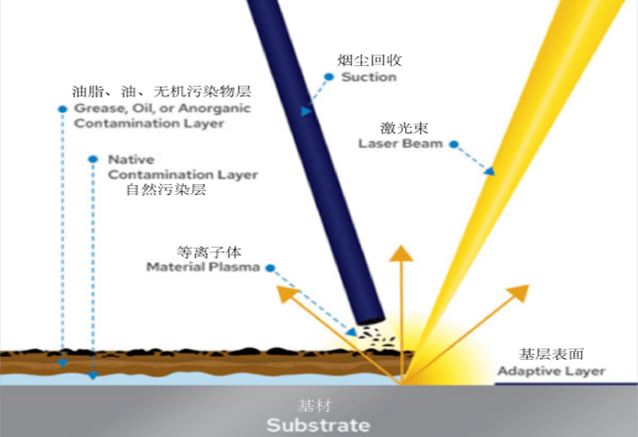
According to the analysis of a large number of experimental results, the laser cleaning mechanism is different according to the difference between the surface attachment and the thermal physical parameters of the matrix. When the thermal physical parameters of the surface attachment and the matrix material are quite different, the laser cleaning mechanism includes: ablation vaporization, thermal vibration and thermal shock mechanism, and acoustic vibration mechanism, such as laser cleaning paint and rubber layers. When the thermophysical parameters of the surface attachment and the base material are not much different, the main ablation vaporization mechanism is at work, such as laser rust removal.
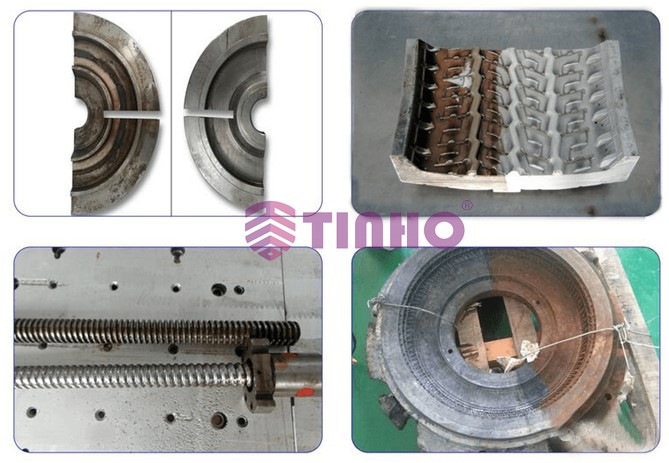
Laser cleaning tire mold
Classification of laser cleaning
There are generally four laser cleaning methods
1. Laser dry cleaning method, which uses pulsed laser direct radiation to decontaminate;
2. The method of laser + liquid film, that is, first deposit a layer of liquid film on the surface of the substrate, and then use laser to explode and decontaminate the liquid film;
3. The method of laser + inert gas, that is, while the laser is irradiated, inert gas is blown to the surface of the workpiece. When the dirt is peeled from the surface, it will be blown away from the surface by the gas to avoid re-contamination and oxidation of the cleaned surface;
4. Use a laser to loosen the dirt, and then use a non-corrosive chemical method to decontaminate.
At present, the first three cleaning methods are mainly used in industrial production. The laser dry cleaning method is more used than the laser + liquid film cleaning method; the fourth method is only seen in the cleaning and protection of artworks.
Laser cleaning features
Compared with the traditional cleaning process, laser cleaning technology has the following characteristics:
1. It is a kind of “dry” cleaning, no cleaning fluid or other chemical solutions are needed, and the cleanliness is much higher than that of chemical cleaning processes;
2. The scope of dirt removal and the scope of applicable substrates are very wide;
3. By adjusting the laser process parameters, it is possible to effectively remove contaminants without damaging the surface of the substrate, so that the surface is as old as new;
4. Laser cleaning can easily realize automatic operation;
5. The laser decontamination equipment can be used for a long time, and the operating cost is low;
6. Laser cleaning technology is a “green” cleaning process. The eliminated waste is solid powder, small in size, easy to store, and basically does not pollute the environment.
The choice of laser
At present, there are many types of lasers, such as CO2 lasers, Nd: YAG lasers, and excimer lasers. All these types of lasers can achieve laser cleaning. But generally speaking, when the high-precision requirements are higher than the large-volume removal or cost requirements, the excimer laser is a more suitable tool. In other cases, CO2 and solid-state lasers are better; for the microelectronics industry, Generally, excimer lasers are used, such as KrF excimer. For mold cleaning, CO2 or YAG lasers are better; for laser coating removal, CO2 lasers are effective, especially TEA CO2 lasers in this field. future. In addition, if the composition of surface contaminants is known in advance, the type of laser can be selected according to the absorption wavelength of the contaminants.
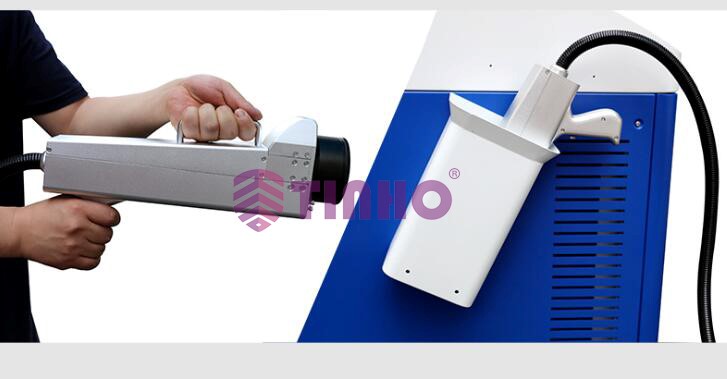
Shanghai Tinho Intelligent Equipment Co., Ltd. is located in Shanghai, As a high-tech enterprise dedicated to R& D, manufacture and sales of inkjet coding & laser equipment, holds more than 20 patents on technology and software to guarantee machine with high quality & high performance, till to now the Tinho full series products included Small character inkjet printer, Laser Marking Machine, Thermal Inkjet Printer, Laser cleaning machine, Laser welding machine already sold well to different country with a good evaluation,if any further assistance or inquiry, welcome to contact us at any time.
Tinho Intelligent
TEL: +86 137 6190 3268 (Whatsapp)
Email: sales@tinhointelligent.com
Web.: www.tinhointelligent.com